Grasping the Art of Welding: Exactly How to Prevent Undercut Welding Issues for Flawless Fabrication Results
By understanding the origin creates of undercut welding and carrying out efficient methods to prevent it, welders can boost their craft to brand-new degrees of quality. In the pursuit of flawless manufacture results, mastering the art of welding to avoid undercut concerns is not just an ability however a necessity for those striving for excellence in their work.
Recognizing Undercut Welding
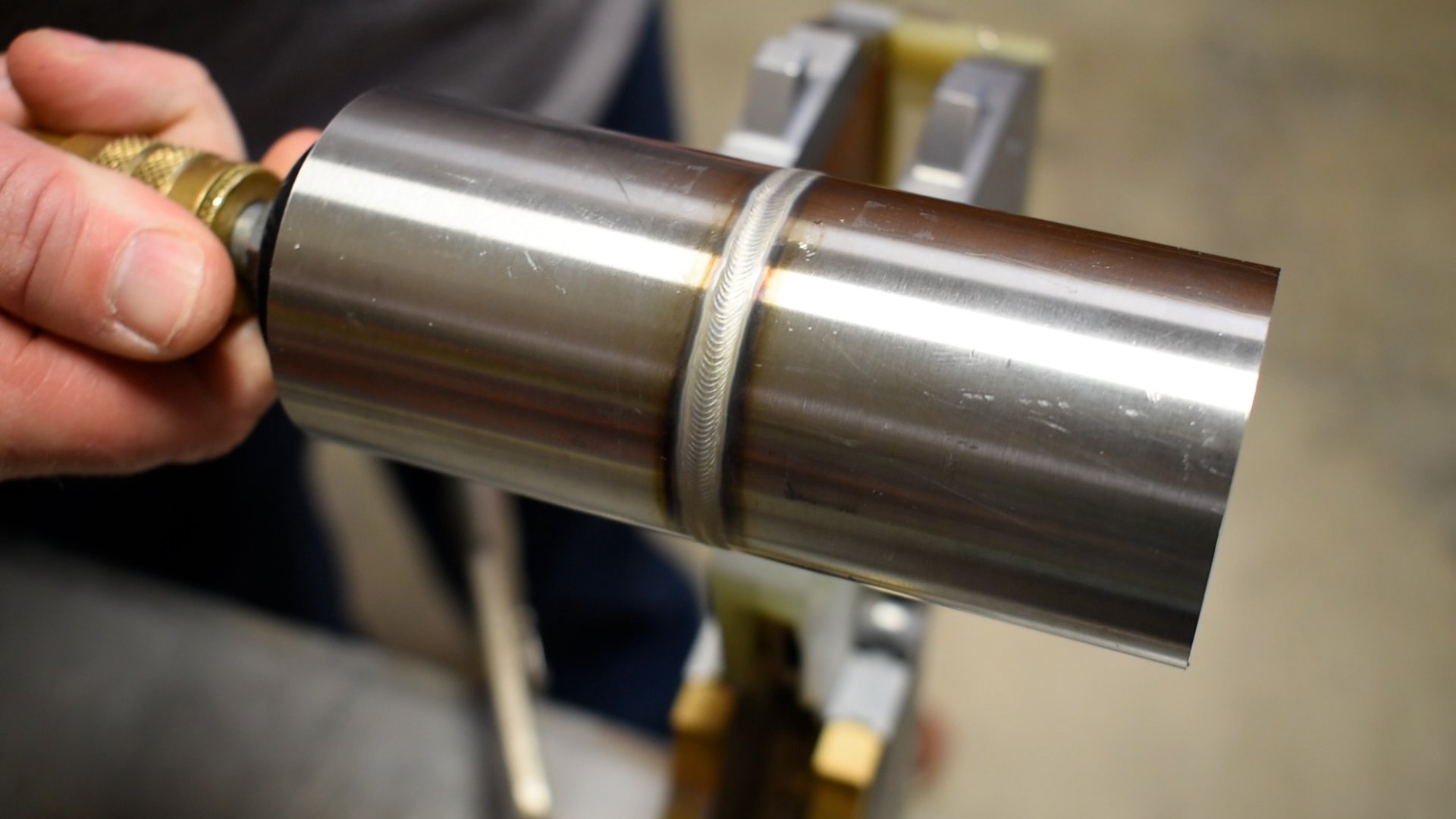
To stop undercut welding, welders must make certain correct welding parameters, such as adjusting the current, voltage, travel speed, and maintaining the appropriate electrode angle. By comprehending the causes of undercut welding and carrying out precautionary procedures, welders can accomplish high-quality, structurally sound welds.
Root Causes Of Undercut in Welding
Understanding the elements that add to damage in welding is important for welders to generate top quality, structurally sound welds. Poor welding current or incorrect welding rate can also contribute to undercut. Comprehending these reasons and implementing correct welding strategies can aid prevent damaging problems, making certain durable and strong welds.
Methods to avoid Undercutting

To minimize the threat of undercutting in welding, welders can use tactical welding techniques focused on boosting the top quality and honesty of the weld joints. One effective method is to readjust the welding criteria, such as voltage, existing, and take a trip rate, to make certain correct warmth input and deposition. Keeping an ideal electrode angle and making certain regular traveling speed can also help prevent undercut. Additionally, making use of the proper welding strategy for the certain joint setup, such as weave or stringer beads, can contribute to reducing damaging. Preventing weld undercut.
In addition, appropriate joint preparation, consisting of guaranteeing tidy base materials without impurities and using the ideal welding consumables, is critical in stopping undercut problems. Using back-step welding strategies and regulating the weld bead account can likewise aid distribute warmth evenly and decrease the risk of undercut. Routine inspection of the weld joint throughout and after welding, as well as carrying out top quality assurance actions, can aid in resolving and spotting damaging concerns quickly. By carrying out these strategies vigilantly, welders can accomplish remarkable fabrication results with minimal undercut flaws.
Importance of Proper Welding Parameters
Selecting and maintaining appropriate welding parameters is essential for achieving successful welds with marginal issues. Welding criteria describe variables such as voltage, present, travel speed, electrode angle, and securing gas circulation price that directly impact the welding procedure. These criteria need to be very carefully changed based on the kind of product being welded, its thickness, and the welding strategy used.
Appropriate welding specifications guarantee the correct amount of warmth is used to thaw the base metals and filler material evenly. If the specifications are set too expensive, it can bring about extreme heat input, creating distortion, spatter, or burn-through. On the various other hand, if the specifications are too reduced, incomplete blend, lack of infiltration, or undercutting might occur.
Quality Control in Welding Operations
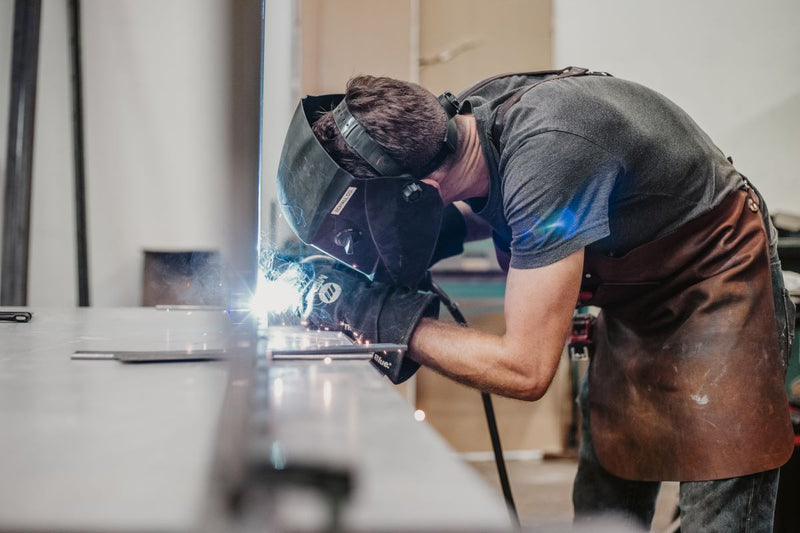
Verdict
Finally, understanding the art of welding needs a comprehensive understanding of undercut welding, its causes, and techniques to stop it. By making sure appropriate welding parameters and executing high quality assurance methods, remarkable fabrication outcomes can be accomplished. It is essential for welders to continually aim for quality in their welding operations to avoid undercut issues and produce high-grade welds.
Undercut welding, an usual flaw in welding processes, takes place when the weld steel doesn't properly fill the groove and leaves a groove or anxiety along the index bonded joint.To stop undercut welding, welders need to make sure proper welding criteria, such as readjusting the present, voltage, traveling rate, and preserving the right electrode angle. Inadequate welding incorrect or current welding speed can also add to damage.To mitigate the threat of damaging in welding, welders can use calculated welding methods aimed at improving the high quality and stability of the weld joints.In verdict, mastering the art of welding requires a detailed understanding of undercut welding, its causes, and strategies to prevent it.
Comments on “How to Avoid Weld Undercut: Vital Tips for Welders”